Stainless Foundry

Investment Casting Vs Sand Casting
In foundry work, there are 12 common types of casting processes. They are: molding in the sand, molding in loam, plaster, dry sand casting, investment casting, lost wax casting, shell molding, vacuum casting, centrifugal casting, and continuous casting. Some examples of special casting molds include investment casting, lost foam casting, metal.
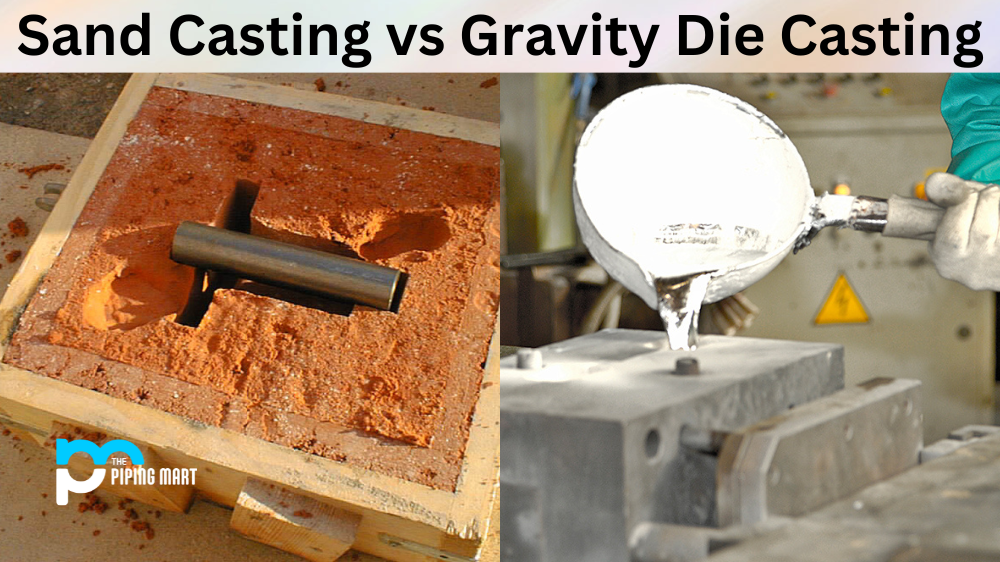
Advantages and Disadvantages of Titanium Valve
August 26, 2023 18 min read Sand casting uses a cavity formed in lightly bonded sand to form a temperature-resilient and reliable tool to allow molten metal to be formed into complex parts. It is a low-tech and relatively simple process that is commonly integrated into the manufacture of complex and technologically sophisticated products.
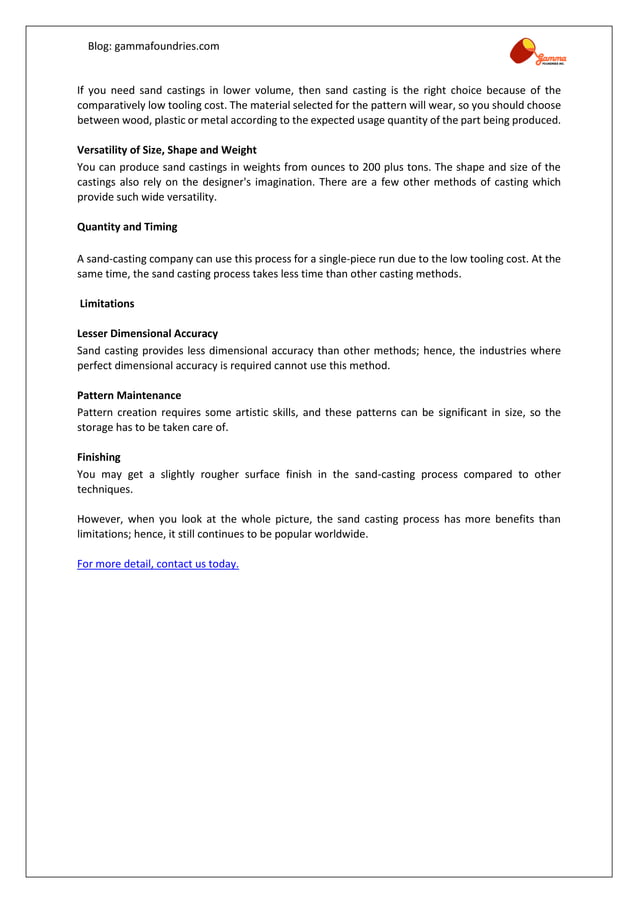
Sand Casting Process Advantages and Limitations
One of the primary disadvantages of sand casting is that it can only produce parts made from low-melting metals, such as aluminium, copper, and zinc. This is because the sand mold must be heated to melt the metal, and if the metal is too high a melting point, it will simply shatter the mold. Shrinkage Issues

The Advantages & Disadvantages Of Using Investment Casting
Advantages of Sand Casting The first advantage of sand casting is its low cost. This makes it ideal for larger production runs because the cost per unit decreases as more units are produced. Also, sand-casting molds can be reused, reducing the cost even further.
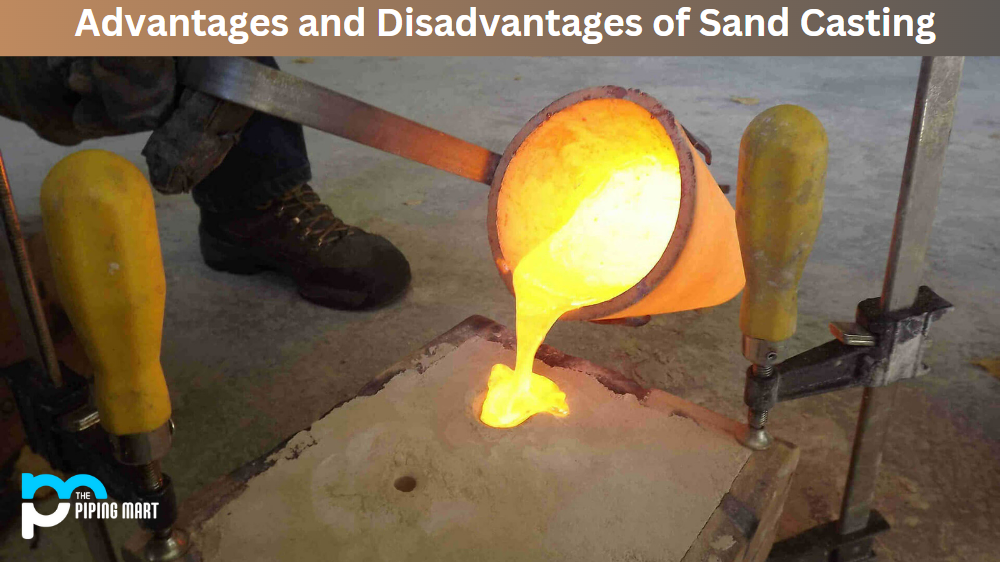
5 Advantages and Disadvantages of Sand Casting
While sand casting has a number of important advantages, there are a few disadvantages you should consider before opting for this type of casting. These include…. Rough texture. Surface finish of the sand casting is somewhat rough compared to parts made using other casting methods. Secondary machining required.
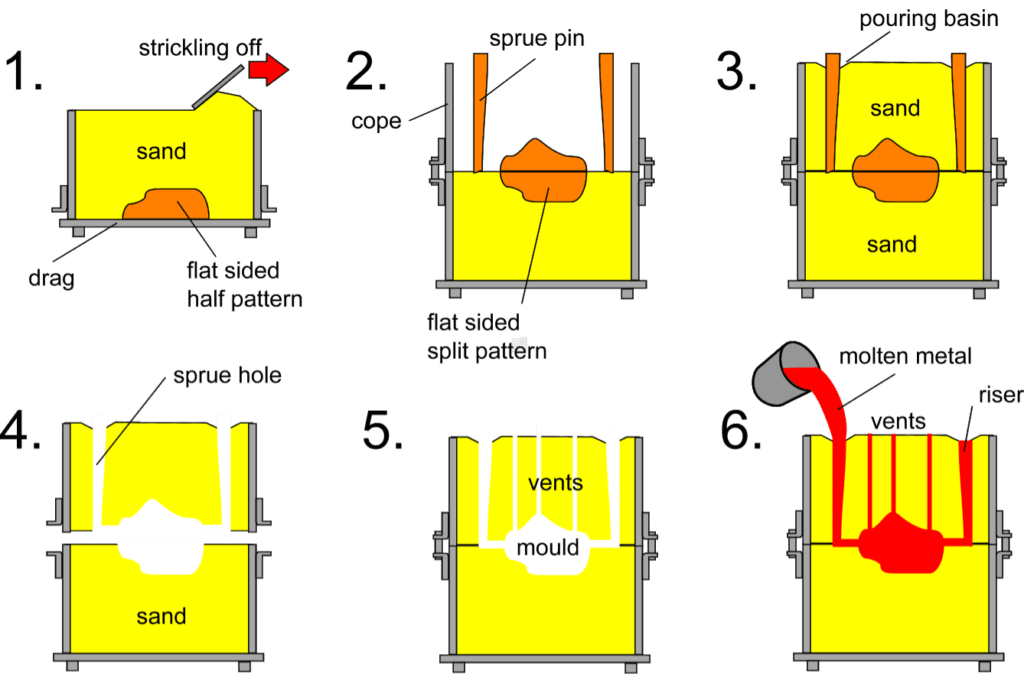
The Most Comprehensive Casting Process Summary Precise Cast
Chapter 3: Types of Casting Sand. Sand casting is a very versatile manufacturing method that provides developers, designers, and engineers with the freedom to create complex and intricate parts with high tolerances. It can be used with any form of metal, which is the reason it is the most common casting process.

Pag Panna Metal TechWhat Is And Different Process
Figure 1: Basic steps in the sand casting process. Image credit: https://en.wikipedia.org. Sand casting is a casting process by which sand is used to create a mold, after which liquid metal is poured into this mold to create a part. To learn about the other forms of casting, visit our article on the types of casting processes.

Advantages of Investment casting Panna Metal Tech
Advantages Of Prototype Casting If you are reading this discussion on sand casting processes, you are likely trying to get a better idea of what method of prototype casting would be best for the product that you have in mind. Prototype casting using a sand casting foundry is best when you might need:
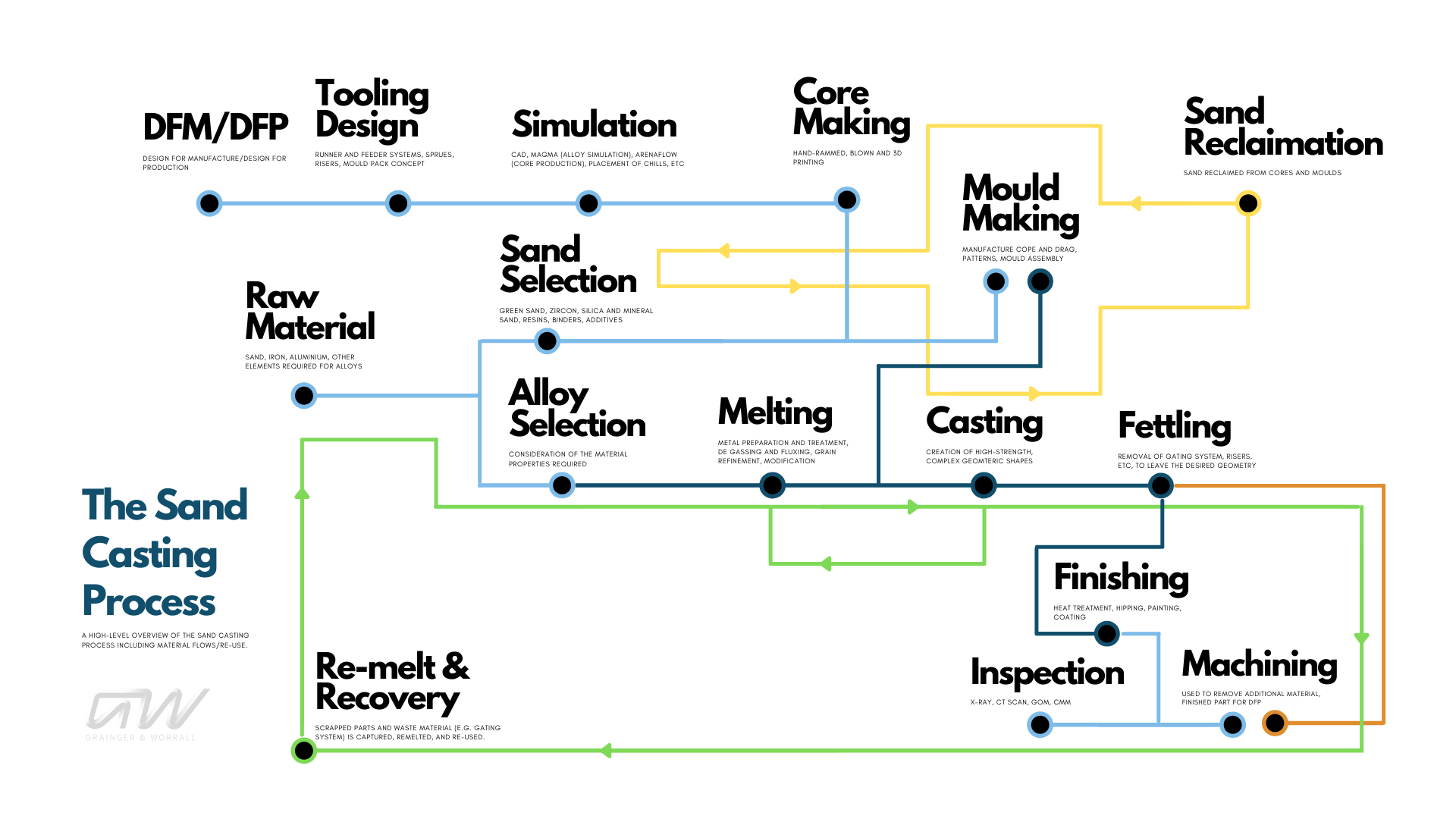
How the sand casting process can help with rapid prototyping
Advantages of Sand casting Simple production process Use common Sand make mould or Pattern out. and ouring into Melten metal liquid into mould or pattern. after cool down, take the part out. Low cost Casting molds the Mould or pattern most is square one. it is simple with low cost. Lower production costs

Advantages and disadvantages of Sand casting It cast, Sand casting, Sand
Advantages & Disadvantages of Sand Casting Sand casting takes advantage of sand's inherent compactability, refractory nature and recyclability to produce relatively inexpensive molds. Sand casting requires a relatively low investment and allows for quick tooling development and part changes at a reasonable cost.

Advantages and Disadvantages of the Metal Casting Process Sinoway Industry Metal Parts
Advantages of Sand Casting: Sand casting is a very old and simple manufacturing process. The production time is very short. Sand casting, or sand molds, differs from other metal casting processes by requiring an easily workable material to make the mold.
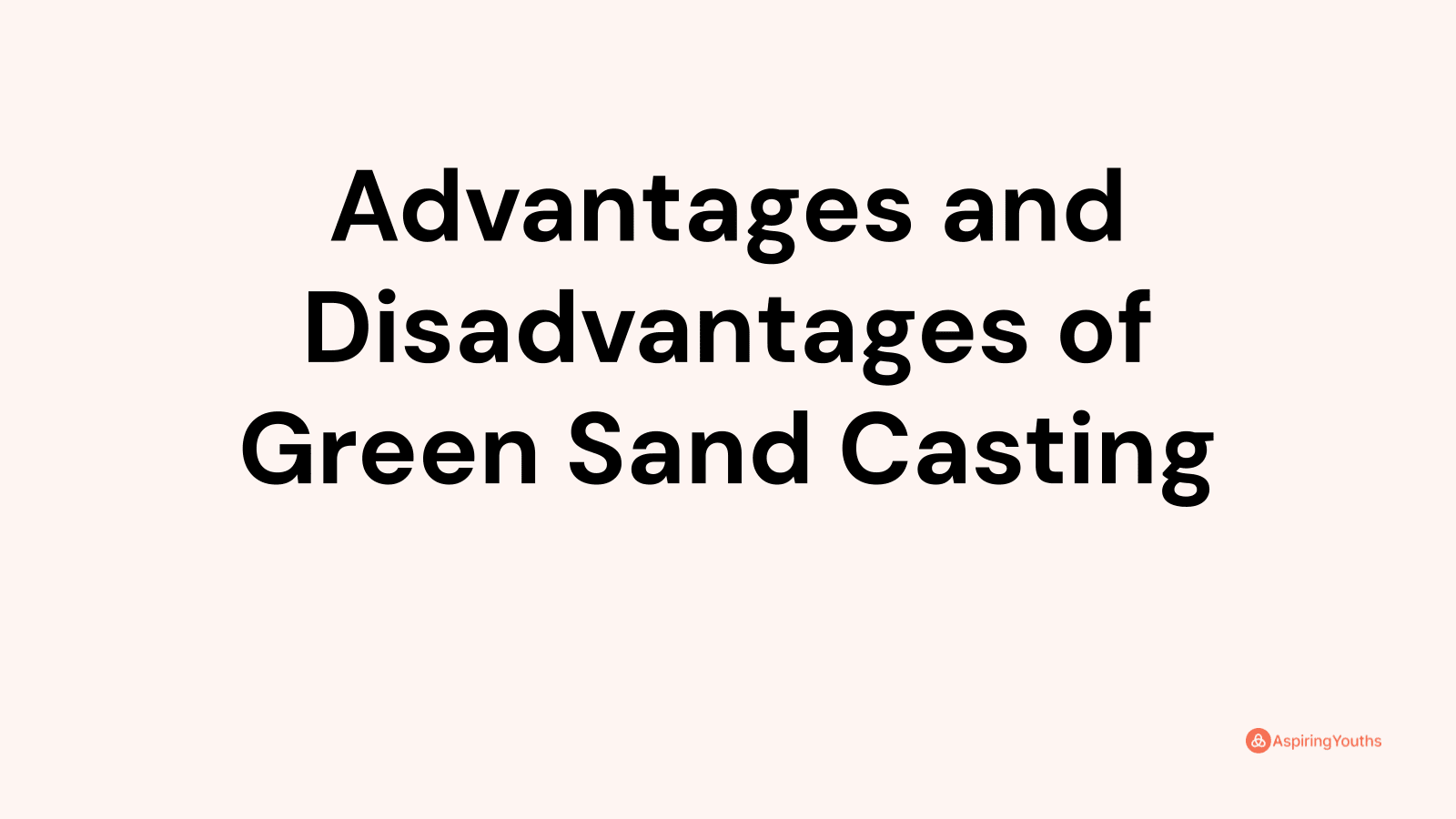
Advantages and Disadvantages of Green Sand Casting
The following are the advantages and disadvantages of Sand Casting: Advantages of Sand Casting Low cost for large parts - Sand casting is affordable, especially for big items. This makes it a cost-effective choice when creating large parts or components.
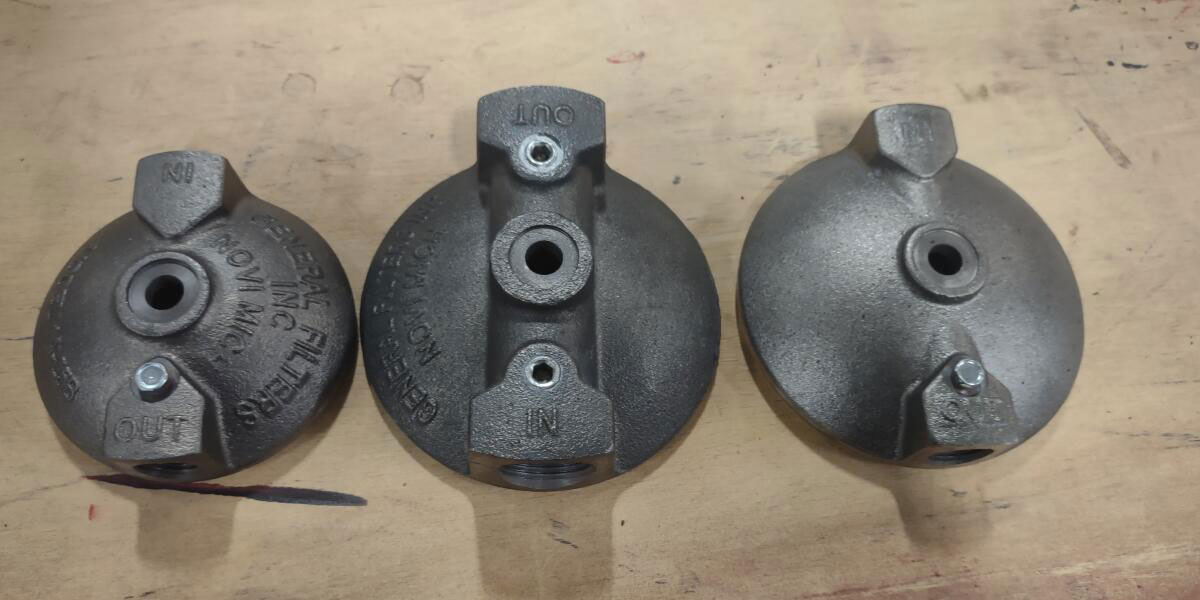
Advantages and Disadvantages of Sand Casting JC Casting
Sand Casting Advantages Castings up to 6,000 pounds (depending on configuration) Gross Weight Lower cost to produce Shorter lead times While investment casting is ideal for highly complex designs - it can cast 1/8-inch walls at the thinnest and work with both ferrous and non-ferrous metals - investment casting does have weight and size limitations.

Stainless Foundry
November 23, 2020 By: Dave Olsen Benefits of Using Sand Casting 1. Nearly any alloy: Sand castings can be readily produced in nearly any ferrous or non-ferrous alloy. Some other casting processes will melt and pour super-alloys in a vacuum, but that is not typically done as a sand casting.
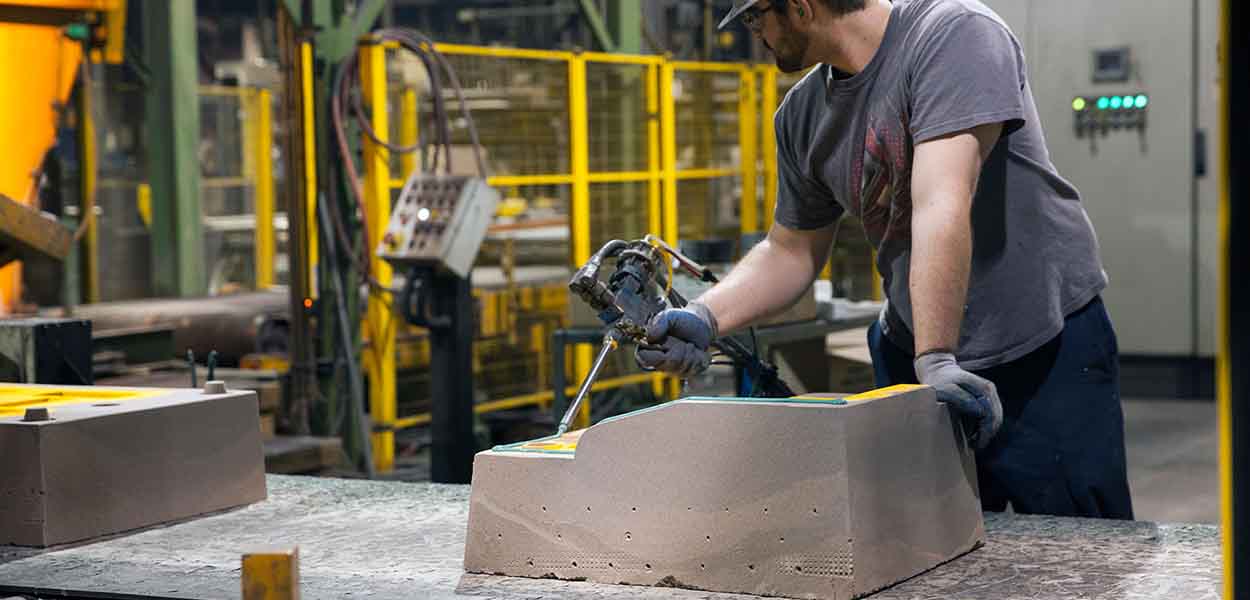
Sand Casting Process Advantages and Limitations MetalTek
Disadvantages of sand casting: A lower degree of accuracy than an alternate method. This process tends to yield products that have a comparatively rough surface finish. Low material strength due to porosity. Surface finish dimensional accuracy is very poor. Defects such as shrinkage, porosity, surface defect, pouring metal defects are unavoidable.
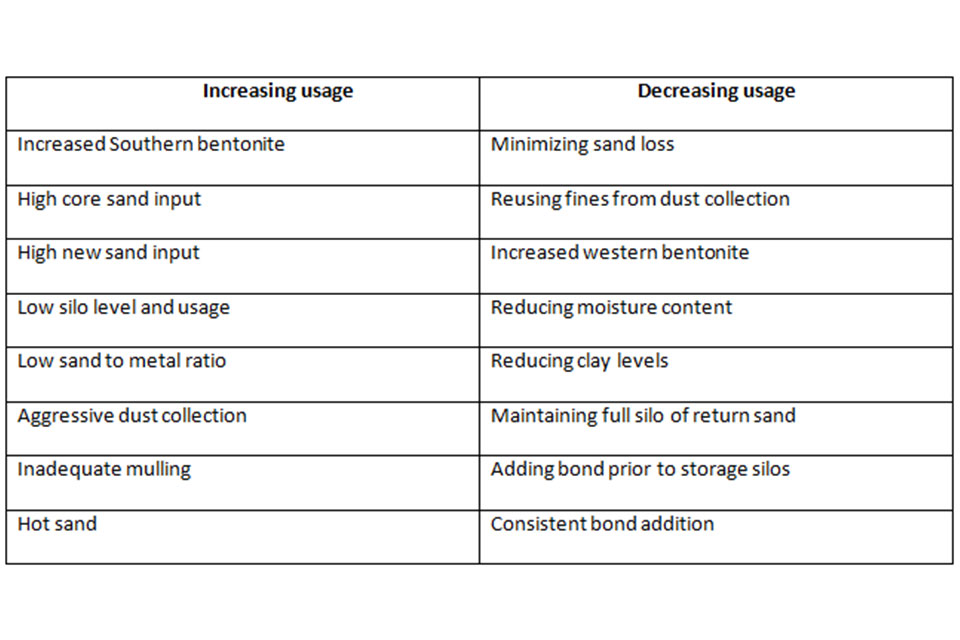
Reducing Bond Usage in Green Sand Systems
Sand casting is used mostly in producing automotive products, such as engine blocks, casings, and housings. Some other advantages of the sand casting process include: Both ferrous and nonferrous metals are used for casting. Low cost of production. Low cost for post-casting tooling. Complex shapes can be produced. Disadvantages. Despite the.